- Main Clients and markets
- Customer Service
- Bearing Selection services
- Bearing Handling Service
- Bearing Fitting Service
- Lubrication Service
- Preload
-
Bearing cleanliness
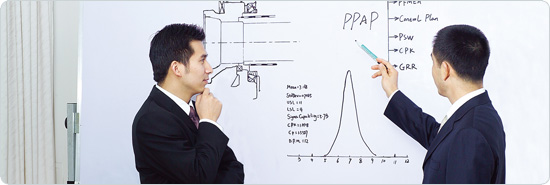
Press mounting require a large force. When attaching the inner ring firmly to the shaft, the force to press-mount an inner ring in the axial direction varies depending on interference and shaft diameter. Moreover, during press mounting work, brinelling indentations may be caused on the raceway surfaces by rolling elements if force is applied to the outer ring. Thus, it is critical to know the fitting surface pressure on mounting performing.
● Pressure and maximum allowable stress
The press fitting force or withdrawal force of the fitted surface, and maximum allowable stress between fitting surfaces which are applied to a solid shaft or hollow shaft, can be expressed by the following equations.
Fit conditions | Equation | Codes (units: N {kgf}, mm) | |
Fitted surface pressure Mpa {kgf/mm2} |
Solid steel shaft/inner ring fit |
![]() |
d: Shaft diameter, inner ring bore diameter d0: Hollow shaft inner diameter Di: Inner ring average groove diameter Δdeff: Effective interference E: Elasticity factor |
Hollow steel shaft/inner ring fit |
![]() |
||
Steel housing/ outer ring fit |
![]() |
D: Housing inner diameter, bearing outer diameter D0: Outer ring average groove diameter Dh: Housing outer diameter ΔDeff: Effective interference |
|
Maximun allowable stress |
Shaft/inner ring fit |
![]() |
Inner ring bore diameter face maximum allowable stress |
Mpa {kgf/mm2} |
Housing/ outer ring fit |
![]() |
Outer ring inner diameter face maximum allowable stress |
● Average groove diameter The average groove diameter is from actual measurement of the bearing or the design data. The right chart can be used to determine the approximate average groove diameter for bearing inner and outer rings. |
|
![]() |
|
Average fit interference as it relates to surface pressure and max. allowable stress | Maximum fit interference as it relates to surface pressure and max. allowable stress |
● Necessary press fit and pullout force
Excessive interference can sometimes produce abnormally large stress in the inner ring, which may cause the inner ring to crack or be otherwise damaged. Euquation below can be used to calculate the necessary pullout force for press fit for inner rings and shafts or outer rings and housings.
Kd= μ · P · π · d · B KD= μ · P · π · D · B |
where,
|
● Press fit and pullout sliding friction coefficient
Friction on the fitted surface differs substan- tially depending on the fitted-surface condit- ions. In general, the value listed in the follow ing table can apply to the values of u. As a general rule, it is desirable to choose a fit for which the maximum stress value may be set to 98MPa or less for bearing steel or, in the worst case, to 127Mpa or less. |
|