- Main Clients and markets
- Customer Service
- Bearing Selection services
- Bearing Handling Service
- Bearing Fitting Service
- Lubrication Service
- Preload
-
Bearing cleanliness
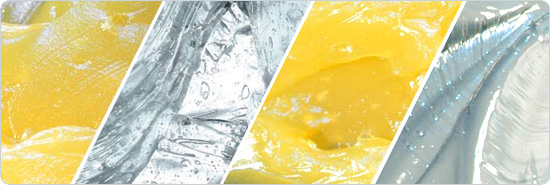
The following lubricating conditions exist in a rolling bearing.
a) Boundary lubrication Under boundary lubrication conditions, load is transmitted via continuous surface contact. In combination with poor lubrication this may lead to extreme wear and premature bearing failure. Some heavy-duty grease containing suitable additives for wear protection can also be considered. b) Mixed lubrication Under mixed-friction lubrication conditions, variable load are transmitted partly between the surface asperities across the roughness peaks in contact with one another, and partly via a lubricant film. Wear protection additives should be used under these conditions to prevent excessive wear. c) Full-film lubrication Full-film lubrication is the optimum lubrication condition characterized by complete separation of the surfaces by a load-bearing lubricant film. Depending on the internal friction of the lubricant, extremely low friction coefficients can be attained. |
![]() |
● Friction
Theoretically, the resistance met by the rolling elements when contacting the bearing raceways is assumed to be of a purely rolling nature. In practice, however, partial sliding may occur between the rolling elements and the raceways. Sliding between the cage and the rolling elements can also occur resulting in churning or displacement of the lubricant.
![]() |
The frictional moments, and hence the friction coefficient The curve of the friction coefficient μ indicates the increase and decrease of the frictional moments that occur in line with a temperature increase and decrease in the bearing. |
● Viscosity ratio
The importance of the oil viscosity for the formation of an oil film is to separate the bearing surfaces and thus for the life of the bearing is dealt with the viscosity ratio K as following:
|
where, K = 3 viscosity ratio V = actual operating viscosity of the lubricant mm2/s V1 = rated viscosity depending on the bearing mean diameter and rotational speed, mm2/s |
Note: The information applies equally to the base oil viscosity of greases.The base oil of viscosity normally used for rolling bearings lies between 15 and 500 mm2/s at 40℃. Greases based on oils having higher viscosities than 1 000 mm2/s at 40℃. Bleed oil so slowly that the bearing will not be adequately lubricated. Therefore, if a calculated viscosity well above 1000 mm2/s at 40℃. is required because of low speeds, it is better to use a grease with a maximum viscosity of 1000 mm2/s and good oil bleeding properties or to apply oil lubrication.