Research & Development>HCH steel tube factory
Research & Development
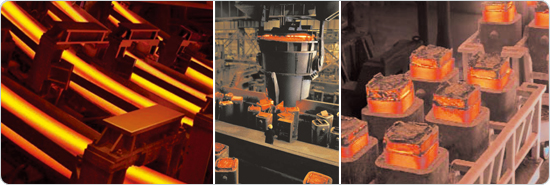
HCH steel tube factory
Deep processing of the material is finished inside the group. HCH’s steel tube factory supplys thousands of tons of bearing material every month.
Product testing includes eddy current (external surfaces), ultra-sonic (internal surfaces). HCH technicians monitor areas, detect air leaks and provide estimated leakage reports. Testing material properties include hardness, strength, toughness and cleanness testing.
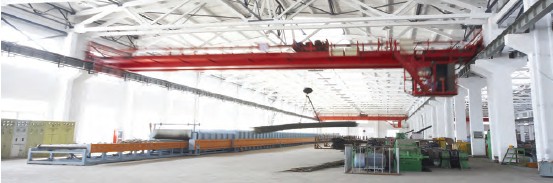
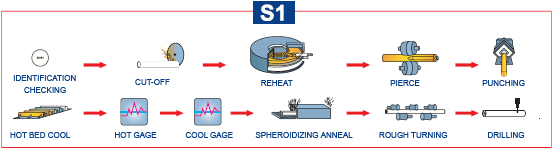
Billet cut off | Billet cut off is used primarily to cut the billet within the length requirement and to obtain metallur- gical samples for testing requirement by the customer’s specifications. |
Reheat furnace | All mills are equipped with a rotary hearth furnace where the product is rotated through a number of heated zones. The furnace is equipped with control systems to automatically adjust furnace temperatures. |
Pierce | This is the heart of the tube mill, where a solid billet is made into a tube with rough OD and wall dimensions. The mill consists of two barrel rolls set at a feed angle that will pull the billet into the mill and rotary forge the steel over an internal tool to form the tube. |
Hot bed cooling | This is the standard process for tubing air cooling, which immediately following piercing on a spe- cial table or hot bed that continuously advances the tubing as additional tubes are finished. Tubing that is hot bed cooled may require additional thermal treatment to obtain optimum machinability or required mechanical properties. |
Spheroidize annealing | This special type of annealing requires an extremely long cycle. Spheroidize annealing is used to produce a globular condition of the carbide and maximum softness for best machinability in some analyses or to maximize cold formability. |
Rough turning | Turned tubing is produced by machining the outside surface of the hot rolled tubing. This process removes surface defects and decarburization from the outside, but the inside diameter surface retains the hot rolled finish. |
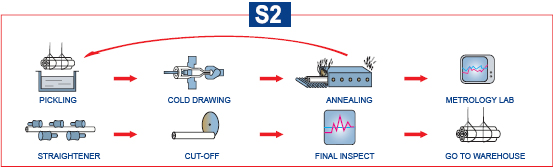
Pickling | Pickling removes the scale formed on the surface of the tube during piercing or heat treatment by utilizing a chemical action in sulfuric acid. After the acid bath, the tubing is rinsed in water. |
Cold drawing | Cold drawn tubing is produced from hot rolled tubes that have been carefully inspected and prop- erly surface-conditioned. Cold drawing consists of pulling a tube through a die and over a mandrel, reducing the diameter and wall thickness. Tubing is cold drawn for one or more of the following reasons: closer dimensional accuracy, better surface finish, smaller sizes than can be hot rolled, or to achieve certain mechanical properties. Cold working also imparts higher strength to the tubing and tends to improve machinability of carbon and lean-alloy steel. |
Annealing | Annealing is heating uniformly to a temperature within or above the critical range and cooling at a controlled rate to a temperature under the critical range. This treatment is used to produce a definite microstructure, usually one designed for best machinability. It is also used to remove stresses; induce softness; and alter ductility, toughness or other mechanical properties. |
Straightener | This process is used to achieve straightness tolerances by a two-roll or multi-roll machine that the tube is rotated through. The tube is helically advanced by the rolls which are adjusted to bend the tube progressively as it moves through the machine. Initial bends and/or bows in the tube are removed, and a straight tube is produced. |
Tube cut off | Tube cut off is used primarily to cut the tubing to the length required and to obtain metallurgical samples for testing required by the customer’s specifications. |
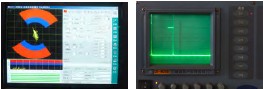
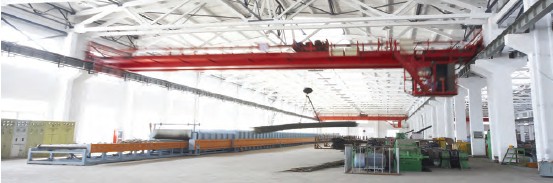