Research & Development>Raw material
Research & Development
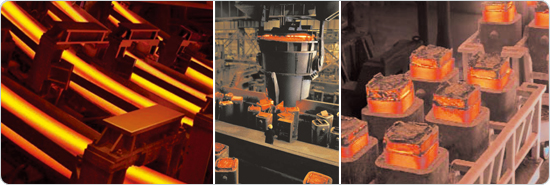
Raw material
HCH applies high refined bearing raw material.
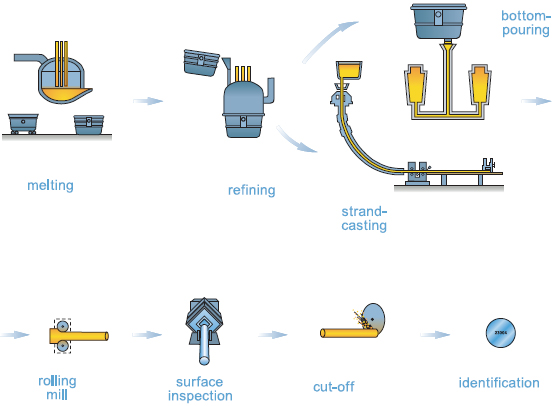
Melting
The steel-making process begins with scrap selection where blend scrap is customed to meet the grade specifications and customer requirements. Highly trained associates constantly monitor scrap for bulk chemistry, density, impurities and residuals. When the molten steel is tapped into a ladle, a slag rake is used to remove the oxidized slag from the heat. Oxygen is removed from the steel at this stage to prevent oxidation that could compromise the quality of the steel.
Refining
The refining process is where the steel is really made. Alloys are also added to get the desired chemistry and degas in order to minimize the levels of entrapped gases in the steel. During this process, the steel is stirred with argon to homogenize the temperature and chemistry of the entire steel heat. The refiners are equipped with Vacuum Arc Degassing (VAD) units that provide the ability to reheat in the ladle. This direct reheat capability allows very tight chemistry control.
Strand cast
The molten steel is poured through a shroud into a 20-ton tundish with a system of dams and weirs designed to optimize metal flow to further enhance steel cleanness. A refractory shroud with an argon seal protects against reoxidation. From the tundish, the steel flows into four separate oscillating molds, again protected from reoxidation through submerged ceramic pouring tubes and mold flux. The mold level is controlled through a closed-loop, throttling slide-gate system to ensure good surface quality. Airmist cooling of the strand is used to gently extract heat during solidification that minimizes thermal stress on the strand.
Bottom Pour
Hot rolled tubing has a surface finish. Light mill oxide covers both the outside and inside surfaces. Hot rolled tubing can be produced to outside diameter and wall dimensions with stated tolerances. Once a steel bloom is produced, it enters a rolling mill to reduce within the size range. Good dimensional size control is maintained on the rolling mill that begins with precise temperature control in the reheat furnace and continues with an in-line, real-time precision gauging system that monitors size through the complete rolling process.
Inspection
The goal is to provide a defect-free hot-rolled steel bar that is extremely reliable. The steel bars are inspected for both surface and internal quality. The system allows inspect down to 0.3mm surface defect tolerances. The inspection process combines thermal-imaging technology for surface inspection with advanced ultrasonic capabilities. These features, along with two-level computer controls, bring advanced product verification.
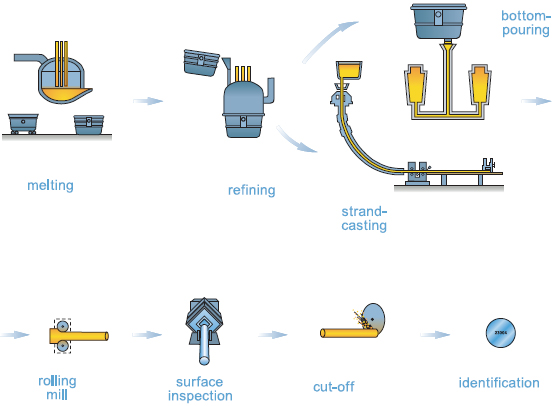
Melting
The steel-making process begins with scrap selection where blend scrap is customed to meet the grade specifications and customer requirements. Highly trained associates constantly monitor scrap for bulk chemistry, density, impurities and residuals. When the molten steel is tapped into a ladle, a slag rake is used to remove the oxidized slag from the heat. Oxygen is removed from the steel at this stage to prevent oxidation that could compromise the quality of the steel.
Refining
The refining process is where the steel is really made. Alloys are also added to get the desired chemistry and degas in order to minimize the levels of entrapped gases in the steel. During this process, the steel is stirred with argon to homogenize the temperature and chemistry of the entire steel heat. The refiners are equipped with Vacuum Arc Degassing (VAD) units that provide the ability to reheat in the ladle. This direct reheat capability allows very tight chemistry control.
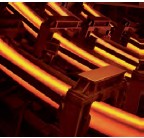
The molten steel is poured through a shroud into a 20-ton tundish with a system of dams and weirs designed to optimize metal flow to further enhance steel cleanness. A refractory shroud with an argon seal protects against reoxidation. From the tundish, the steel flows into four separate oscillating molds, again protected from reoxidation through submerged ceramic pouring tubes and mold flux. The mold level is controlled through a closed-loop, throttling slide-gate system to ensure good surface quality. Airmist cooling of the strand is used to gently extract heat during solidification that minimizes thermal stress on the strand.
Bottom Pour
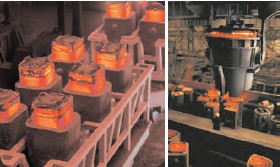
The bottom-pour process creates some of the world’s cleanest air-melt steels. Ingot molds are “big end up” that means the tapered end is down to optimize internal cleanness. To ensure cleaner steel, the steel stream is shrouded during teeming by an inert atmosphere to prevent reoxidation. A pre-measured mold flux is added into each mold to further protect the steel from reoxidation and enhance surface quality. Each mold has a hot-top to keep it in a liquid state while the ingot is fed. The mold flux and hot-top system is designed to maximize cleanness and minimize the chemical segregation of the ingot. HCH steel ball material is 100% applied with this process
Rolling
Hot rolled tubing has a surface finish. Light mill oxide covers both the outside and inside surfaces. Hot rolled tubing can be produced to outside diameter and wall dimensions with stated tolerances. Once a steel bloom is produced, it enters a rolling mill to reduce within the size range. Good dimensional size control is maintained on the rolling mill that begins with precise temperature control in the reheat furnace and continues with an in-line, real-time precision gauging system that monitors size through the complete rolling process.
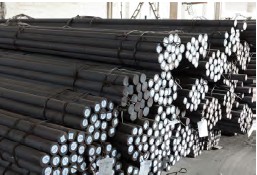
The goal is to provide a defect-free hot-rolled steel bar that is extremely reliable. The steel bars are inspected for both surface and internal quality. The system allows inspect down to 0.3mm surface defect tolerances. The inspection process combines thermal-imaging technology for surface inspection with advanced ultrasonic capabilities. These features, along with two-level computer controls, bring advanced product verification.