Manufacturing & Quality>On site assessment (OSA)
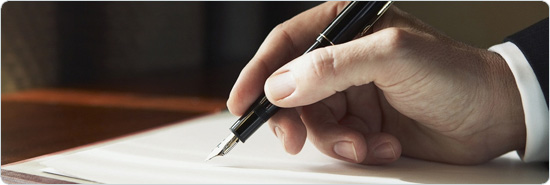
On site assessment (OSA)
The OSA, along with commercial and technical assessment, is part of HCH’s supplier approval process and should be applied in the following situations- Before any business is awarded to a new supplier to HCH- Whenever there is a significant change in an approved supplier’s operations, such as plant relocation or change of ownership. Periodically, as determined by HCH, in order to ensure continuation of supplier’s quality management systems. Also, OSA may be completed for a currently approved supplier as a prerequisite for other Part Qualification activities, especially where the design or manufacturing process of the new components is significantly different with earlier approved components. HCH is used to evaluate a supplier's quality systems and is an integral part of the HCH supplier approval process.
Partial Credit | Full Credit | Assessment Item | Observations and Notes | Supplier Response |
1. Is the supplier ISO or TS registered? | ||||
2. Is there a published Quality Policy and is it to all personnel (e.g., Quality Manual)? | ||||
3. Is there an organization chart with responsibilities assigned? | ||||
4. Are the quality control systems adequately documented? Work Instructions; Stan- dard Operating Procedures; Quality Objectives; External Documents | ||||
5. Do systems and processes focus on defect prevention in all areas? | ||||
6. Has training been provided for each job function or operation according to requirements? | ||||
7. Is there a documented internal audit process | ||||
8. Are systems and audit results periodically reviewed by management? | ||||
9. Is there a Corrective Action system and does it have means to track | ||||
10. Do systems and audit deficiency corrective actions have a due date | ||||
11. Is there a Preventative Action system and does it have a mean to track. | ||||
12. Is there a process established for the control of records and system documentation? Policy for control of quality records; Retention policy or matrix; Revision control process for quality documents; Customer documents identified and their distribution controlled. | ||||
13. Are the environmental conditions in the laboratory and work areas adequate for the work performed? | ||||
14. Are control charts effectively used throughout production areas? | ||||
15. Is there evidence of control charts leading to actions? | ||||
16. Are inspection and process instructions adequate,controlled and available to respective personnel? | ||||
17. Are workmanship standards available in the form of controlled written standards, visual exhibits (color chips) and / or samples? | ||||
18. Is there a process for identifying and managing finished goods inventory in a FIFO manner? | ||||
19. Is there a maintenance plan for all equipment and tooling? | ||||
20. Does the organization have a system for identification, traceability, preservation and handling of product throughout all phases of production? | ||||
21. Is non-conforming material sufficiently identified and segregated at all stages of the process? | ||||
22. Are adequate records maintained? Do records show that re-worked parts / ma- terials are re-inspected? If remanufacture / reprocessed material is used, is there adequate identification and checking to specifications? | ||||
23. Are root cause and corrective action identified to prevent recurrence of reported failures and quality problems? | ||||
24. Are gages and test / inspection equipment, including customer owned gages and equipment adequately maintained, calibrated and stored? | ||||
25. Are controls in place to assure actions are taken in the event of calibration failure? | ||||
26. Does the organization provide adequate training for personnel using gages? | ||||
27. Does the organization ensure statistical studies(Gage R&R) are conducted to analyze the variationpresent in the results of each type of measuring and test equipment system? | ||||
28. Are process capability studies performed including Failure Mode Effects Analy- sis (FMEA's)? | ||||
29. Are in-process defects charted and analyzed to detect problem areas and de- fect trends? Is in-process and final verification performance data collected, ana- lyzed & charted against year-over-year improvement targets? | ||||
30. Does the manufacturing process improvement continually focus upon control and reduction of variation in product characteristics and manufacturing process parameters? | ||||
31. Does the organization have a defined process for problem solving leading to root cause identification and elimination? Examples of problem solving processes. | ||||
32. Are there programs that internally target productivity and continual improvement? | ||||
33. Is there a formal system for review and validation of design input requirements? | ||||
34. Is design output documented in terms of requirements, calculations, and analysis? | ||||
35. Is there a formal procedure for controlling design changes including review and approval responsibilities? |