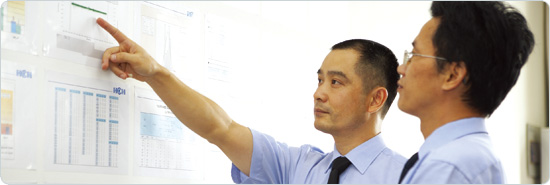
1. Review of requirements related to the product: Product requirements are defined. Reviewing the order and contract requirements and resolving the detailed problem to ensure HCH bearings meet specific requirements.
2. Quality management system audit: HCH Internal Audit department audits its quality management system to verify compliance with technical specification and any additional quality management system requirements, also audit each manufacturing to determine its effectiveness.
3. The department should audit products at appropriate stages of production and delivery to verify conformity to all specified requirements, such as product dimensions, functionality, packaging and labeling, at a defined frequency.
4. Continuous Improvement: Evidence demonstrates the use of data (ie: First Pass Yield, Final Test, In-process Cpk, etc.), past experience, and lessons learned may be requested to show continuous improvement of quality management system.
SHOPFLOOR AUDIT Receiving Inspection, Manufacturing Operation, Post-Process (as applicable), Packaging, Shipping |
||
PREPARATION FOR AUDIT (Documents Required) | Available (Yes/No) | Dates and Revisions of Documents |
1) Are receiving inspection instructions available and accurate, as appropriate? | ||
2) As defined in the Control Plan, is appropriate sample size and frequency maintained at receiving inspection? | ||
3) Are control plan inspections and process steps covered in the manufacturing/work instructions? | ||
4) Are manufacturing instructions approved according to the plant’s procedures? | ||
5) Are manufacturing instructions readily available to the operators? | ||
6) Do the operators follow the manufacturing instructions for the station they are running? | ||
7) Do manufacturing instructions tell the operator what to do when they find a non-conforming part? | ||
8) Is non-conforming product properly controlled? | ||
9) Is there an approved rework instruction for any rework/ repair being performed? | ||
10) Do operators follow written rework instructions? Are parts re-inspected after rework. | ||
11) Are Process or Quality Alerts, as appropriate, being followed? Are the Alerts readily available to the operator? | ||
12) Are in process and/or Lot Acceptance Tests being con- ducted at their specified frequencies? |
Mistake Proofing and Gages | ||
PREPARATION FOR AUDIT (Documents Required) | Available (Yes/No) | Dates and Revisions of Documents |
1) Are inspection results documented and retrievable ? | ||
2) Is mistake proofing verified at the start of every shift? | ||
3) Is mistake proofing verified at the start of every shift? | ||
4) Are all gages updated to the corresponding approved product release level? Do all gages comply with the ap- proved Gage Control Drawing/Specification? |
||
5) Are gages being used according to instructions? | ||
6) Are all gage calibrations current? | ||
Statistical Process Control | ||
1) Are statistical controls used as required in the control plan? Is their evidence to show that someone is review- ing and reacting to the data? |
||
2) When an out-of-control or out-of-spec condition is found, is there documentation indicating the actions taken to correct the situation or contain the issue? |
||
3) Is process stability at or above Cpk targets for critical and significant characteristics or are plans documented to reduce variation? |
||
4) Are continuous improvement action plans available and being implemented? | ||
Identification, Traceability, Packaging, Maintenance, Training, Cleanliness, Safety | ||
1) Are product builds traceable as identified in the Con- trol Plan? | ||
2) Does packaging and labeling meet customer specifications? | ||
3) Is preventive maintenance / PM for the line being per- formed to schedule? | ||
4) Are operators trained prior to operating a station, and is documented evidence readily available? | ||
5) Is tagging of material required? If so, is material tagged per the plant procedures? | ||
6) Are the premises maintained in a state of order, cleanliness, and repair? Are 5Sprinciples adopted? Is Personal Protective Equipment available and worn ac- cording to Factory rules? |
||
Non-Conforming Product, Corrective Action and Lessons Learned | ||
1) For past corrective actions; are the improvement ac- tions still required, effective,and maintained? | ||
2) Are the findings from DOCK AUDITS resolved in a timely manner? |