Manufacturing & Quality>Production Part Approval Process
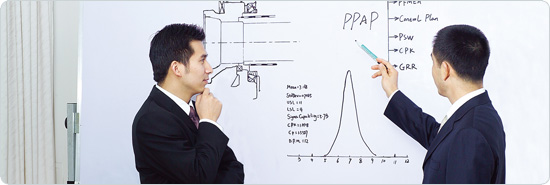
Production Part Approval Process
PPAP is a part of Advanced Product Quality Planning. The purpose is to determine whether all engineering design and specification requirements are properly understood by the Supplier and the process has the potential to produce product consistently meeting these requirements during an actual production run and at the quoted production rate.
PPAP Process Flow
An Example
Part Submission Warrant:
Part Submission Warrant (PSW) is a document on which an approval is formalized. To submit Part Submission Warrant (PSW) for approval along with other documents for verification prior to approval is required. All of the measurements and test results show conformance with drawings and specification requirements must be verified and that all required documentation are available.
Situations Required Notification
It is important to identify any changes that might affect the further processes at next customer or ultimate purchaser of the vehicle or component. Therefore, in the following additional situations, the changes must be notified. The written documentation should be addressed to the approving authority.
Situations Where Notification Is Not Required
Notification and submission of PPAP is not required for the situations described in the following situations:
1. Changes do not affect customer fit, form, function, and durability or performance requirements.
2. Identical gauge replacement (Gauges replaced) as a part of a gauge maintenance or calibration system.
PPAP Process Flow
An Example
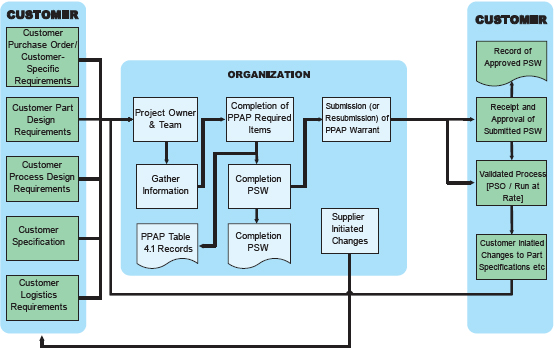
No. | Requirements |
1 | Design Records. |
2 | Engineering Change Documents, if any |
3 | Customer Engineering Approval, if required |
4 | Design FMEA ( If Supplier is responsible for Design ) |
5 | Process Flow Diagram |
6 | Process FMEA. |
7 | Control Plan. |
8 | Records of Compliance Customer Specific Requirements |
9 | Part Submission Warrant (PSW) |
10 | Material Performance Test Results |
11 | Initial Process Study |
12 | Qualified Laboratory Documentation |
13 | Appearance Approval Report (AAR) – if applicable. |
14 | Sample Product |
15 | Master Sample |
16 | Checking Aids. |
17 | Records of Compliance Customer Specific Requirements |
18 | Part Submission Warrant (PSW) |
Part Submission Warrant:
Part Submission Warrant (PSW) is a document on which an approval is formalized. To submit Part Submission Warrant (PSW) for approval along with other documents for verification prior to approval is required. All of the measurements and test results show conformance with drawings and specification requirements must be verified and that all required documentation are available.
Situations Required Notification
It is important to identify any changes that might affect the further processes at next customer or ultimate purchaser of the vehicle or component. Therefore, in the following additional situations, the changes must be notified. The written documentation should be addressed to the approving authority.
No. | Requirements | Clarification of requirement |
1 | Use of other construction or material than was used in the previously approved part or product. | For example, other constructions as documented on a deviation or included as a note on the design record and not covered by engineering change. |
2 | Production from new or modified tool (Except for perishable tools), dies, molds, patterns, etc., including additional and replacement tooling. | This requirement only applies to tools which due to their unique form or function, can be expected to influence the integrity of the final product. It is not meant to describe standard tools (new or repaired), such as standard measuring devices, drivers (manual or power etc.) |
3 | Production following upgrade or rearrangement of existing tooling or equipment. | Upgrade means the reconstruction and / or modification of a tool or machine or to increase the capacity, performance, or change in the existing function. Not to be confused with normal maintenance, repair or replacement of part for which no change in performance is to be expected and post repair verification methods has been established. Rearrangement is defined as to the activity, which changes the sequence of product / process flow from that documented in the Process Flow Chart (PFC). This includes addition of new manufacturing processes. Minor adjustments of production equipment may be required to meet safety requirements such as, installation of protective covers, elimination of potential ESD risks etc. |
4 | Production from tooling & equipment transferred to a different plant site or from an additional plant site. | Production process tooling and / or equipment transferred between buildings or facilities at one or more sites e.g. Any m/c shifted by supplier within floors in the same building, then PPAP needs to be reviewed. |
5 |
Change of supplier for parts, nonequivalent materials, or services (e.g. Heat Treatment, Plating) |
Material and services should be approved. |
6 | Product produced after the tooling has been inactive for volume production for twelve months or more. |
For product that has been produced after tooling has been inactive for twelve months or more. Notification is required to Team Leader /nomi- nated representative – when the part had no active purchase order and the existing tooling has been inactive for volume production for twelve months or more. The only exception is when the part has low volume e. g. specialty vehicles, Certain PPAP requirements for service parts may be specified. |
7 | Product & Process changes related to com- ponents of the production product manufac- tured internally or by suppliers. | Any change that affects requirements for fit, form, function, performance and/or durability requires notification to the Team Leader /nominated representative . |
8 | Changes in test/inspection method – new technique (no effect on acceptance criteria) | For change in test method, the supplier should submit the study so as to verify that the new method has measurement capability equivalent to the old method. |
Situations Where Notification Is Not Required
Notification and submission of PPAP is not required for the situations described in the following situations:
1. Changes do not affect customer fit, form, function, and durability or performance requirements.
2. Identical gauge replacement (Gauges replaced) as a part of a gauge maintenance or calibration system.