Manufacturing & Quality>Advanced Product Quality Planning
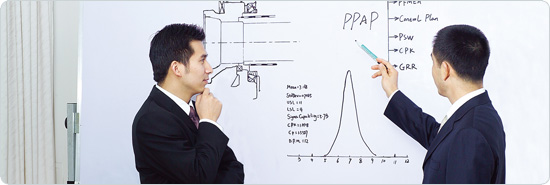
Advanced Product Quality Planning
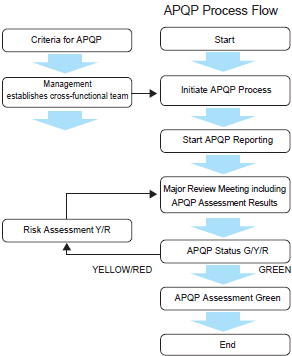
Goal:The goal of APQP is to facilitate communication with all persons involved in a programme and ensure that all required steps are completed on time, at acceptable cost and quality levels.
Applicability:
APQP is a requirement of all activities and must be applied to the following:
● New Product.
●Changed / modified product.
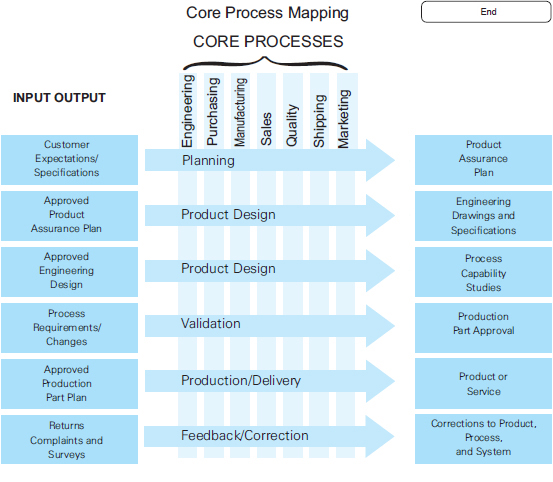
APQP Status Report
The APQP Status Report summarizes the status for the 23 APQP elements. The status report facilitates communication between Suppliers. It also provides a dated record that future programmes can reference.
Team Members | Company / Function | Contact No. / E-mail | ||||||
Build Level | MRD | Quantity | Concurred | PIST % | PIPC % | |||
No. of SC | No. of CC | |||||||
APQP Elements | GYR Status | Focus Element Rating | Program Need Date | Completion Date | Resp. Engineer Initial | Remarks |
Sourcing Decision | ||||||
Customer Input Requirements | ||||||
Design FMEA | ||||||
Design Review(s) | ||||||
Design Verification Plan & Report | ||||||
Subcontractor APQP Status | ||||||
Facilities, Tools and Gages | ||||||
Prototype Build Control Plan | ||||||
Prototype Builds | ||||||
Drawing and Specifications | ||||||
Team Feasibility Commitment | ||||||
Manufacturing Process Flow Chart | ||||||
Process FMEA | ||||||
Measurement System Evaluation | ||||||
Pre-Launch Control Plan | ||||||
Operator Process Instructions | ||||||
Packaging Specifications | ||||||
Production Trial Run | ||||||
Production Control Plan | ||||||
Preliminary Process Capability Study | ||||||
Production Validation Testing | ||||||
Production Part Approval (PSW) | ||||||
PSW Part Delivery at MRD | ||||||
COMMENTS : |
Note: If the programme is considered to be low risk, the APQP leader may skip certain APQP elements.
Green Yellow-Red (GYR) Status communicates the progress towards the successful completion of an APQP element by the Program Need Date. The Program Need Date is the last possible date an element can be completed and not adversely affect quality or timing of the Program. The “GYR Status” column of the report shows the assessment for each element. Definitions for Green, Yellow, and Red are as follows:
Status | Meaning |
Green |
Date / quality of the element are not at risk Start of production is not at risk |
Yellow |
* Date / quality of the element are at risk * Start of production is not at risk * Corrective measures must be defined |
Red |
* Date / quality of the element not be observed * Start of production is at risk * Corrective measures must be defined |