Manufacturing & Quality>New Component Introduction
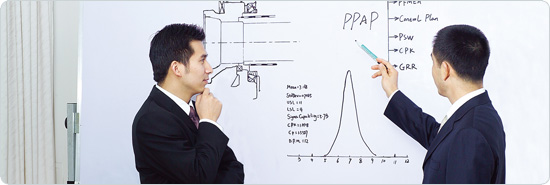
New Component Introduction
NCI is HCH's production part approval process and applies to both purchased and HCH manufactured parts. For purchased parts all NCI-related interface between HCH and the supplier is handled via the Parts Qualification Requirements document (PQR).
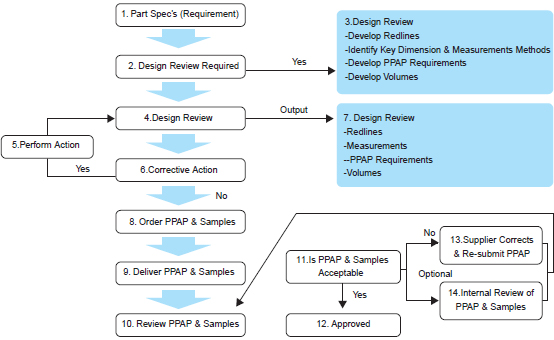
NCI is a stage gate review process that ensures that changes of all sizes and complexity are approved by management, projects are appropriately resourced and sucessfully accomplished project goals.
Process/Design Change Request
Note: Design Verification Plans and Reports include the following tests
● Engineering Development Tests: Performed during product design for functional development, for detecting time dependent failures.
● Design Verification Tests : Performed to demonstrate that the design samples meeting production intent environmental, functional, reliability and durability requirements
● Production Validation Tests: Performed to demonstrate that the design samples from the production environment meet all requirements
similar to Design Verification tests and assure that no adverse variables have been introduced.
● Continuous Conformance Tests: Performed on an ongoing basis to assure contained compliance to all Product & Process requirements.
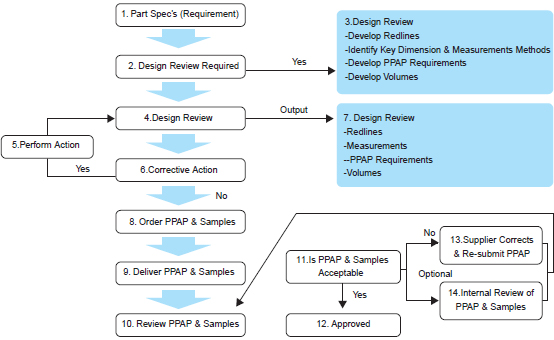
NCI is a stage gate review process that ensures that changes of all sizes and complexity are approved by management, projects are appropriately resourced and sucessfully accomplished project goals.
Process/Design Change Request
Change Type (circle one): Process Design |
Origination Date: |
Description of Change |
Reason for Change |
Affected Product(s) |
Affected Process(es), If known |
Risks/ Containment Actions |
Qualification, Validation Plan and Results |
Customer Approvals (work authorization to proceed to next review) |
Engineering: Date: |
Quality: Date: |
Customer Input Requirement |
To generate the Customer Input Requirements, design goals (as specified by customer survey) are translated into tentative and measurable design objectives. Reliability and Quality goals are established by the HCH product engineers based on the following elements: - Prior model product and process concern history - Customer wants and expectations - Programme objectives - Reliability bench-mark |
Design Records | HCH will retain Controlled copies of Product Drawing / Engineering Standards received from customer. Supplier should retain controlled copies of customer approved drawings / standards. The part drawing of details for assembly and relevant standards should also be supplied by customer. CAD data, Math data should also be retained. |
Design Reviews |
Design Reviews are regularly scheduled meetings led by the design responsible activity and must include any affected areas, such as Engineering, Manufacturing personnel etc. The review process includes the followings: ● A series of verification activities that are more than engineering inspection. ● An effective method to prevent problems and misunderstandings. ● Provide a mechanism to monitor progress and report to the management (including the review of APQP open issues) |
Process/Design Change Request | It is possible that during product development a change is suggested in the product, part or tooling by R&D / Engineering but not yet incorporated in the drawing / standard. The HCH Process/Design Change Request form is used to request a change in manufacturing process or design materials. |
Design Verification Plan &Report | The Design Verification Plan & Report (DVP&R) is a document listing the engineering evaluations, tests, and reports required to establish a design fit for use in the intended environment and meets the customer driven objectives and the intent with which the product / process was designed. The design verification plan has a correlation with the Customer Input Requirement. |
Design Approval | In case if the supplier requires certain changes in customer drawing or specification, prior to the submission for part approval should obtain R&D / Engineering approval. The request regarding the change should be communicated through the respective customer Materials Management. If the changes are not incorporated in the drawing pertaining to the submission, the approved document must be submitted along with the PSW. |
Operator Process Instructions | Operator Process Instructions describe the details of controls and actions that operating personnel must perform to produce quality products. Operator Process Instructions de- scribe all process steps necessary to produce a quality product, and include all essential visual aids and/ or detailed instructions to support the production operators. |
Sample Product | Supplier should submit samples of the product to customers, unless agreed and mentioned on the Part Submission Warrant, along with Applicability Matrix. The sample products should be duly checked for dimensional results and the same to be used for fitment trial. |
Production Trial Run | The production trial run is a validation of the effectiveness of the manufacturing and assem- bly processes using production tooling, equipment and environment (including production operators), facilities and cycle times. Output of the Production Trial Run is used for Produc- tion Part Approval and Quality Planning Sign-Off. |
Note: Design Verification Plans and Reports include the following tests
● Engineering Development Tests: Performed during product design for functional development, for detecting time dependent failures.
● Design Verification Tests : Performed to demonstrate that the design samples meeting production intent environmental, functional, reliability and durability requirements
● Production Validation Tests: Performed to demonstrate that the design samples from the production environment meet all requirements
similar to Design Verification tests and assure that no adverse variables have been introduced.
● Continuous Conformance Tests: Performed on an ongoing basis to assure contained compliance to all Product & Process requirements.