Manufacturing & Quality>Supplier acceptance form (SAF)
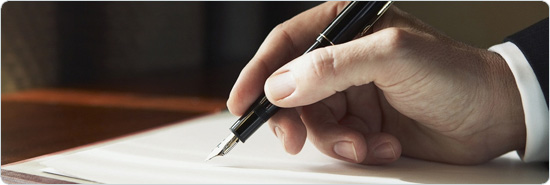
Supplier acceptance form (SAF)
We ask that the appropriate Leaders within your organization review the manual and take the appropriate actions to become fully compliant.
● Supplier Scorecard
This is a process to develop relationships through a supplier evaluation process that promotes communication and continuous improvement throughout the entire product cycle. Involvement, commitment, trust, cooperation, and teamwork are the underlying principles that will guide our quest for achieving customer satisfaction. A routine reviews of the Supplier'sScorecard is a tool used by suppliers and HCH to aid in the communication process.
Note: Please be aware of other sector specific scorecard expectations. Contact your sector quality or sourcing representative for details.
● G Y R Status
Green – “G” ratings given indicates that the element is complete and meets all expectations.
Yellow – “To be considered”, a risk assessment and a recovery plan must be in place for the element. “Y” ratings indicate a need for Programme management attention.
Red – “R” signifies the Programme is at risk and needs immediate management attention. To reflect improvements of a RED element’s status after the PND, progress to GREEN will be shown by a second entry in brackets.
By signing and returning this page to the appropriate HCH commodity manager, I hereby acknowledge receipt of HCH’s Supplier Quality Manual, on behalf of my company. |
Company Representative & Title: |
Company Name: |
Company Address: |
City, State, Zip |
Country: |
Phone: |
Signature Authorized Supplier |
Date: |
● Supplier Scorecard
This is a process to develop relationships through a supplier evaluation process that promotes communication and continuous improvement throughout the entire product cycle. Involvement, commitment, trust, cooperation, and teamwork are the underlying principles that will guide our quest for achieving customer satisfaction. A routine reviews of the Supplier'sScorecard is a tool used by suppliers and HCH to aid in the communication process.
Pot. Pts | Category | Sub-Categories | Result | Note |
40 | Quality | Monthly & YTD PPM (20pts) | ||
Quality SCARs Issued (20pts) | ||||
20 | Delivery | Delivery SCARs Issued (20pts) | ||
20 | Productivity | Proactive vs Non-responsive(20pts) | ||
20 | Customer Service | Service (20pts) |
Note: Please be aware of other sector specific scorecard expectations. Contact your sector quality or sourcing representative for details.
● G Y R Status
The “GYR Status“ Report |
|||
Risk |
Financial Stability |
G= No risk |
|
Supply Agreement |
Contract |
G= In place |
|
Non-Disclosure Agreement |
G= In place |
|
|
Bailment |
G= In place or Not Applicable Y= In negotiation |
|
|
Standard Pay Terms |
G= Yes |
|
Green – “G” ratings given indicates that the element is complete and meets all expectations.
Yellow – “To be considered”, a risk assessment and a recovery plan must be in place for the element. “Y” ratings indicate a need for Programme management attention.
Red – “R” signifies the Programme is at risk and needs immediate management attention. To reflect improvements of a RED element’s status after the PND, progress to GREEN will be shown by a second entry in brackets.